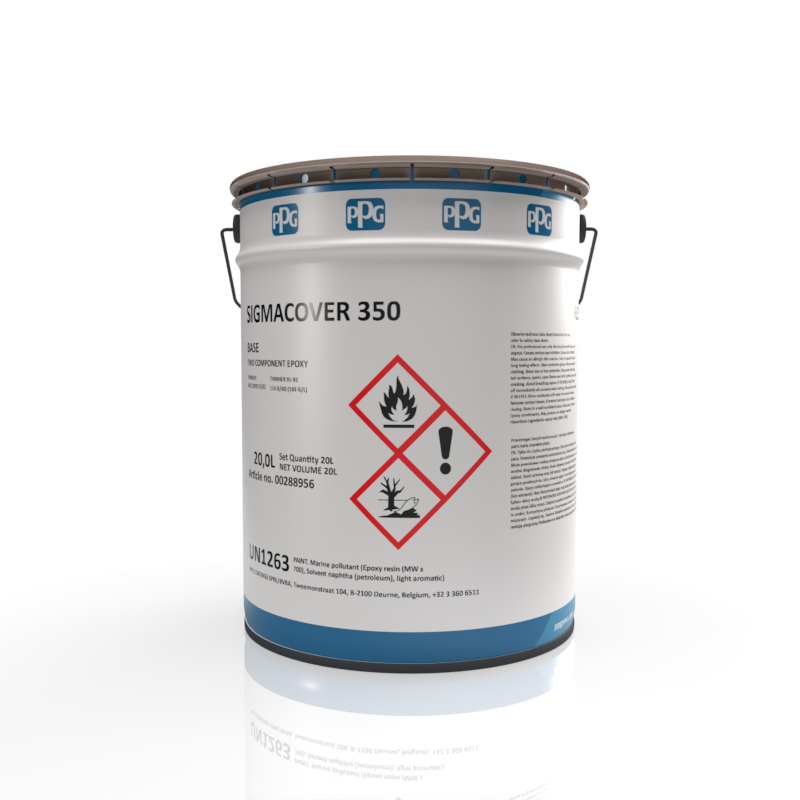
Orders before 12pm dispatched same day.
Opening Hours - Mon-Thurs: 08.00-16.30 - Fri: 08.00-15.00 - Sat-Sun: Closed
Orders before 12pm dispatched same day.
Opening Hours - Mon-Thurs: 08.00-16.30 - Fri: 08.00-15.00 - Sat-Sun: Closed
PPG - Sigmacover 350 - An advanced Epoxy Primer for superior protection against corrosion. Sigmacover 350 is a two-component, a high-performance primer/finish engineered to provide unparalleled protection for a wide range of surfaces.
Custom Colour
Please enter your required colour into the box below and click Submit ColourPPG - Sigmacover 350 - An advanced Epoxy Primer for superior protection against corrosion. Sigmacover 350 is a two-component, a high-performance primer/finish engineered to provide unparalleled protection for a wide range of surfaces.
Key Features include;
Exceptional Durability: Sigmacover 350 boasts exceptional resistance to abrasion, impact, and chemical exposure, making it the ideal choice for protecting critical surfaces from wear and tear.
Corrosion Resistance: This advanced epoxy coating acts as a powerful barrier against corrosion, effectively preventing rust and degradation caused by moisture and harsh atmospheric conditions.
Versatile Application: Suitable for various substrates, including steel, concrete, and other metals, Sigmacover 350 ensures seamless coverage and adherence on a wide range of surfaces.
Rapid Curing: With a quick curing time, Sigmacover 350 minimizes downtime and allows for faster project completion, maximizing efficiency and productivity.
Environmentally Friendly: Committed to sustainability, Sigmacover 350 is designed with environmentally conscious materials, reducing its ecological impact while delivering top-notch performance.
Easy Application: Sigmacover 350 offers user-friendly application, making it convenient for both professionals and DIY enthusiasts to achieve a flawless finish.
Ideal Applications: Ideal for ships, offshore structures, and maritime equipment, providing robust protection against saltwater and extreme weather conditions. Perfect for industrial facilities, machinery, and equipment, guarding against chemical exposure, abrasion, and harsh manufacturing environments. Essential for bridges, pipelines, and other critical infrastructure projects, offering long-term protection against environmental factors.
Sigmacover 350 is trusted for its exceptional performance and reliability. Whether you need to safeguard marine assets, industrial machinery, or critical infrastructure, Sigmacover 350 delivers superior protection, ensuring your investments are shielded from the elements and preserving their value for years to come. Invest in Sigmacover 350 today and experience the ultimate in surface protection.
Recommended Substrate Conditions and Temperatures
Substrate Conditions
Substrate Conditions of Concrete for Thinned Version
Coated Concrete
Substrate Temperature and Application Conditions
Instructions For Use
Mixing ratio by volume: base to hardener 80:20 (4:1)
Application
Air spray
Recommended thinner
Volume of thinner
5 - 10%, depending on required thickness and application conditions
Nozzle orifice
1.8 – 2.0 mm (approx. 0.070 – 0.079 in)
Nozzle pressure
0.3 - 0.4 MPa (approx. 3 - 4 bar; 44 - 58 p.s.i.)
Airless spray
Recommended thinner
Volume of thinner
0 - 5%, depending on required thickness and application conditions
Nozzle orifice
Approx. 0.48 – 0.53 mm (0.019 – 0.021 in)
Nozzle pressure
15.0 MPa (approx. 150 bar; 2176 p.s.i.)
Brush/roller
Recommended thinner
Volume of thinner
0 – 5%
Note: 10 - 15% when applied as a primer direct to concrete
Cleaning solvent
Data sheet
Specific References
No customer reviews for the moment.